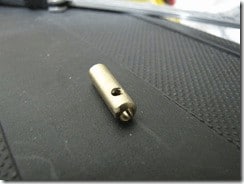
Dear friends, what I want to share this time is the experimental results of machining brass parts with Roland MODELA MDX-20, a desktop 3-axis CNC milling machine. According to the official specifications, copper is listed to be one of the machinable materials of the MDX-15/20. In spite of that, if you have been curious to inspect what is inside this desktop CNC machine, you will find that it is using steel wires and pulleys to pull the X-axis and the Y-axis, instead of using a screw rod. Because of that, when the cutting force is too strong, the mechanics cannot withstand the forces and the tool offsets from the programmed tool path.
About the Experiment:
Fabrication of a substitute of 1/8″ tool holder for MDX-15/20, which has an outer diameter of 6 mm and an inner diameter of 3.175 mm (or 1/8 inches).
Raw material: A solid copper bar with an outer diameter of 5.9±0.1mm
Tool path: Cut the inner hole of 3.175mm through a spiral-down path
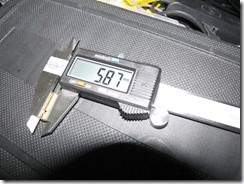
Experimental results:
Custom tool holder Assembly with a 3.175 mm milling bit
Cutting the metal really is not a joke, the blades of the 3 mm milling tool used for the experiment has been blunted, and it seems to be reimbursed (tears). While processing, the stainless steel-made tool, and the brass workpiece became hot, so it is necessary to continuously drip the lubricating fluid to cool down them. In addition, it was found that the error in the z-axis was large, and the depth of the inner hole was far less than that specified in the tool path, and the accumulated error was more than 1 mm. The reason is that the stage of the MDX-15/20 did not have sufficient strength, and the entire stage was elastically deformed when the cutter was pressed down to the brass workpiece.
Fortunately, the shape is simple this time, the required dimensions can be achieved by repeating the same milling path. If it is a complex three-dimensional shape, it will be quite disregarded deformed.
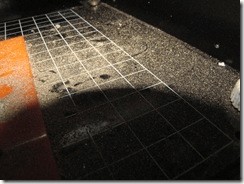
In summary, the desktop CNC machine Roland Modula MDX-15/20 is quite suitable to make a circuit board by removing the copper layer from a laminated PCB bakelite board; but it is obviously not a tool for cutting a solid metal with a certain thickness. The limiting factors include:
- Insufficient stiffness of the x-axis, y-axis, and the stage, causing deformation and displacement of the tool-workpiece coordinates.
The spindle speed is low, the cutting power is insufficient, and the machining time is long.
This experiment took a total of 2 days, the tool holder produced had very poor tolerances. The cutting tool was also seriously damaged. It is totally not worth. The experiment just left a pile of copper shavings and nasty copper smell.
I am afraid that I won’t talk about metalworking again in the coming days.
Or one day, 3D metal printing will be generalized and will reshape our concept of metalworking.
If you have any issues about the machine, you can visit our page FAQ for Roland Modela MDX-20 to find more solutions or leave your questions in the comment section of the FAQ page.
If you enjoy this post, please share it on Facebook and Twitter. You might also support us by making a donation through Ko-fi.